Hydro Turbine / Generator Monitoring
Wind, Solar, Wave and Hydro power generation systems are all increasingly being used to mitigate the unavoidable environmental impact of more traditional generating technologies, like Fossil and Nuclear fueled power generation, and the resulting change of focus has resulted in operational differences for which it is likely that the equipment was never designed.
To complicate matters further, the resulting financial restrictions imposed on unit operators have brought downward pressure to bear upon maintenance budgets and support infrastructure. Moving forward, the inevitable resulting equipment reliability issues must be addressed by plant owners and operators alike if they are to continue operating reliably and efficiently.
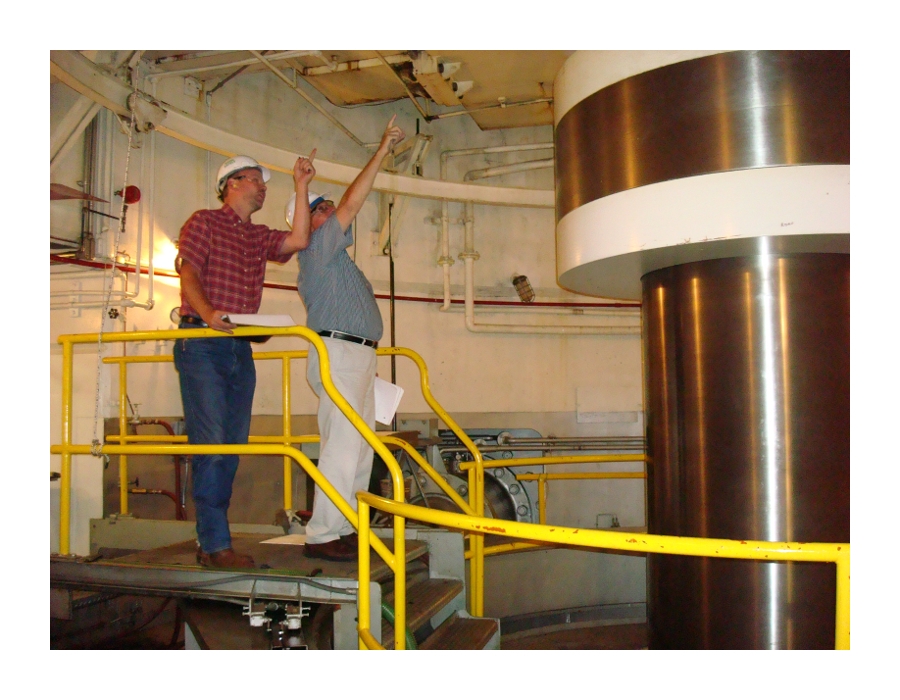
This effect is particularly noticeable within the Hydro Generating sector, where despite having one of the lowest incremental generation costs, previously reliable and long lasting generating units originally designed for base loading duty, are now being used for peaking duty, and are incurring multiple starts and stops each day. This situation is exacerbated still further for Pumped Storage units, which are experiencing many starts and stops per day, resulting in unforeseen stresses on mechanical and electrical components and systems, and in these changed circumstances, condition monitoring for Hydro Turbine / Generation units has never been more important!
More about Hydro Turbine Monitoring – click here
IMPView®Zeefax has introduced a new software product to accompany the 35954U SNet-to-USB interface, and have branded it using the established IMPView® name, which was originally owned and used by Solartron, and which is now owned by Zeefax under the technology transfer agreement recently completed between Zeefax and Mobrey.
The new IMPView® for Windows™ is a configuration, test and data transfer tool designed to allow both existing users and those intending to install new Isolated Measurement Pod (IMP) based data acquisition networks, to use IMPs with modern processor technology. It also includes data sharing and translation using industry standard data protocols – including OPC and MODBUS – to external historians and data collectors.
The new IMPView® supports multiple 35954U modules units into multiple USB ports on a single machine, thereby providing a device for consolidation, manipulation and re-transmission of a combination of acquired data from multiple existing – or new – S-Net networks.
More about IMPView® – click here
PowerPAC™PowerPAC™ is an advanced Data Acquisition and Display software product, designed to meet the rigorous requirements expected from modern Data Acquisition systems. The many configurable features and comprehensive on-line analysis capabilities – including turbine performance, balance-of-plant and emissions indexes – make it ideal for use in process, power and petrochemical plants, but it is equally at home in the laboratory or for specialist research applications.
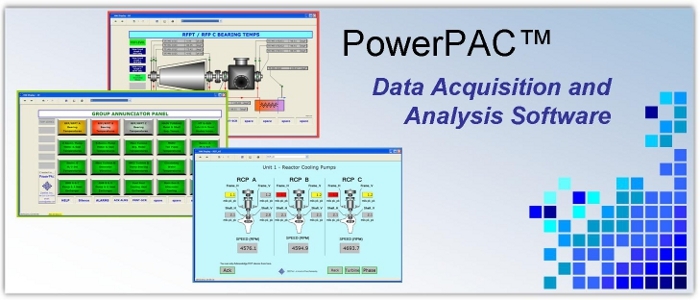
PowerPAC™ provides highly versatile and capable data acquisition, for both stand alone applications and when forming part of a fully integrated Turbine Supervisory or general plant monitoring installation.
Designed for use on PC-based systems running Windows™, this fully integrated package is highly optimized for use within industrial settings, and is ideal for Plant Performance Monitoring, Emissions Monitoring and other general Condition Monitoring applications.
IMP Software OptionsZeefax has been associated with the IMP system since the original launch by Solartron in the early 1980s, and since that time, we have designed, configured and installed a large number of Operator Information Systems (OIS) in a range of industrial environments – including power, process and heavy metals.
The IMP system was originally designed for installation in robust industrial environments without any additional protection and this has proven to be a major and unique selling point over the years, making the installation quick, easy and cost effective for the thousands of companies and locations around the world which still have them installed.
Following our acquisition of the S-Net/IMP system and the subsequent re-launch, Zeefax is now able to offer new manufactured products from the range, and we have plans to release more in the future.
A key and important element of any system is the design and selection of products and sub-systems, including sensors, signal conditioning modules, communication and display products. As a system integrator, Zeefax have gained a wealth of experience in configuring and implementing complex systems where no one product was available to meet the need.
In any system, the most visible part is the operator display, and Zeefax have invested years of development into creating software products and modules to meet the diverse needs and wants of our customers. The result of this can be seens in the two flagship software products – PowerPAC and the new IMPView described here.
IMP Repair and Calibration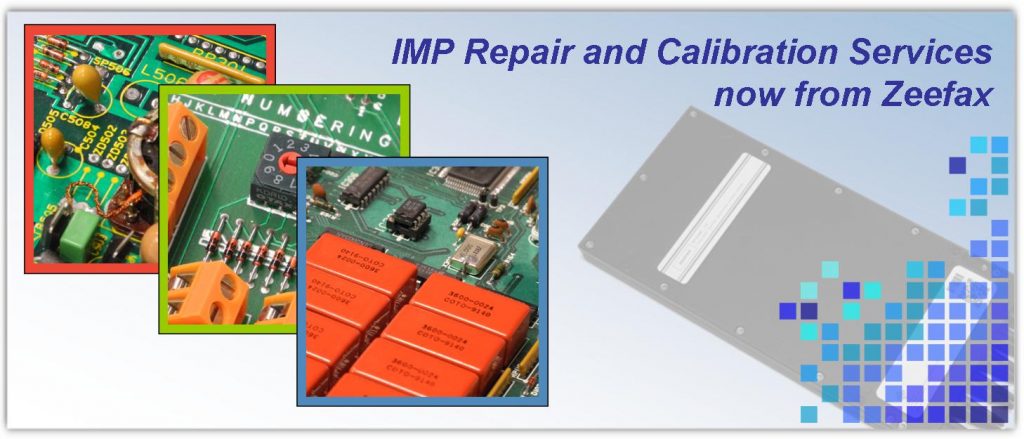
In an important strategic move, Zeefax has been able to acquire an encompassing selection of spare parts, tooling and most importantly, the expertise, and will now be able to provide comprehensive repair, calibration and support services for the Isolated Measurement Pod (IMP) range of products.
More about IMP repair and Calibration – Click here
Radial Vibration MonitoringVibration is simply a measurement of the components of oscillatory motion, and is typically expressed in terms of peak-to-peak displacement, peak velocity or peak acceleration. The particular parameter used is partially based on the environmental conditions at the site to be monitored, but is also conditioned by the speed of rotation, the type of bearing to be monitored, the parameter required and and the potential for damage if failure might occur.
More about Radial Vibration Monitoring – click here.
Thrust MonitoringIt is one of the most critical measurements in rotating machinery, in that if the thrust bearing should fail for any reason, the rotating shaft would then be permitted to move, and the resulting rotor-to-stator contact will inevitably have serious consequences for the machine. Such incidents can become financially overwhelming – considering the cost of the turbine rebuild and the associated loss of production – and can also be a serious hazard to the Health and Safety of plant personnel.
Current best practice indicates that to adequately monitor thrust position, dual probes are recommended to achieve the level of reliability required for this important parameter. The main benefit of the dual probe arrangement is the redundancy provided in case of failure of one or other of the probes, but also in some cases, particularly if being used for tripping, voting may be used to prevent spurious trip events. Often, thrust probes are installed inside the machine bearing case and are inaccessible from the outside while the machine is running, therefore, it is vital that any installed probes will perform reliably up until the next scheduled outage.
More about thrust monitoring – click here.
Differential ExpansionDuring the transient phases of operation of a rotating machine, (start-up or cool-down) heat soaking and dwells are used to ensure that thermal expansion or contraction to not cause rotor-to-stator contact.
It is common to use non-contact probes (eddy current probes) attached to the turbine casing to observe the rotor, thereby measuring the difference between the movement of the rotor and the casing as they thermally expand.
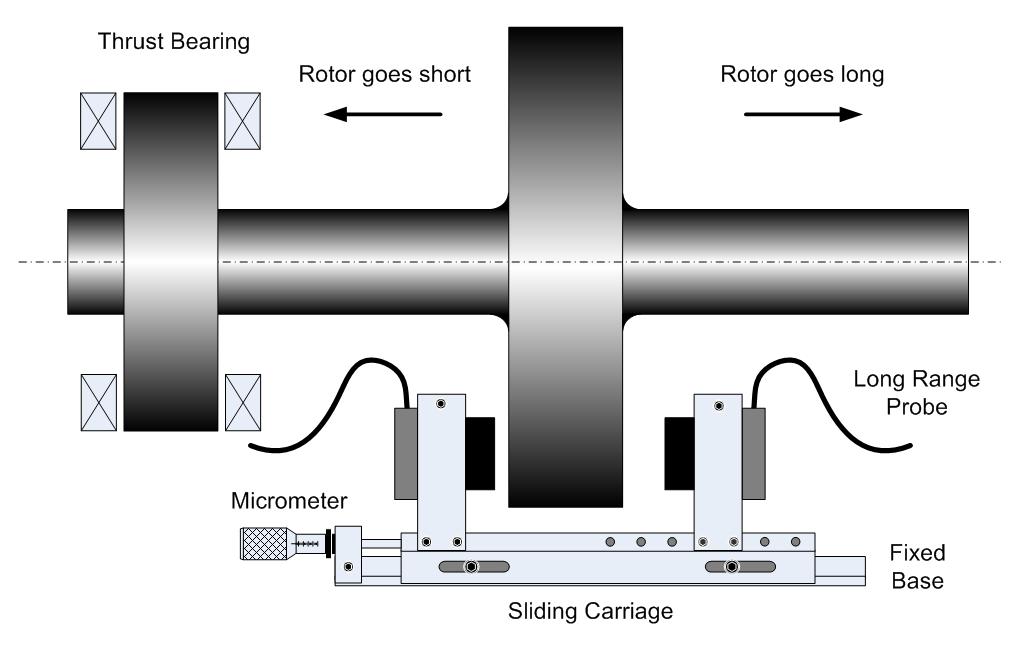
Eddy current probes are available with measurement ranges up to 1/2 inch or more, and so sometimes this measurement can be made conventionally, i.e. with the probe directly observing a rotating flange or collar. However, in some instances, the range required is greater than the probe range available – due to physical or target area limitations, and therefore an alternative method must be implemented to measure the differential expansion.
More about Differential Expansion – click here
Casing Expansion MonitoringDuring the start-up and run-down phases of any large machine, the turbine case (stator) and the enclosed rotating turbines (rotor) will tend to expand or contract at different rates, and therefore monitoring the CE is vital to ensure that serious turbine damage does not occur.
The location of the fixed or pin point on a particular machine will determine the requirements for casing expansion and will also dictate the type of transducers or sensors used; in practice, non-contact eddy current probes will usually be used for the rotor, and LVDTs will often be used for the stator or casing.
More about Casing Expansion (CE) – click here
Rotor / Casing Position MonitoringPerhaps surprisingly, large turbines are typically designed to operate with internal clearances of the order of 5-30 mils of radial clearance and perhaps 100 to 500 mils clearance axially, so when considering the size of a typical turbine/generator machine, this may seem to be incongruous. However, maintaining these clearances during turbine startups and run downs is vital and requires careful monitoring to avoid rubbing or rotor-to-stator contact which will invariably wreck the turbine.
During start-up when the turbines are thermally cycled from ambient temperature – in the region of 60°F – up to working temperature, which might be as high as 1000°F or more, they undergo significant dimensional changes, often expanding by as much as 1 to 1.5 inches axially. It is for this reason that axial clearances should be carefully monitored, and the machine should be protected against unexpected casing or differential expansions or thrust collar movements.
Typically, the axial clearances are monitored using non-contact sensors (eddy current probes) which are usually located close to and directly monitor the position of the shaft thrust collar relative to the thrust bearing. These values are typically small (less than 100 mils) and therefore, a standard eddy current probe is usually sufficient for the purpose. But moving firther away from the thrust bearing, the thermal expansion values increase significantly due to the large masses and long turbine shafts, and therefore either a different type of sensor is usually required or a mechanical ‘amplifier’ is used to increase the range of a short range eddy current probe. For larger expansions of stationary parts, a Linear Variable Differential Transformer (LVDT) can be used, or for rotating parts, ramps machined onto the rotating shaft or in some cases, cantilever ‘amplifiers’ are used to increase the range of a standard eddy probe.
VibraTool™As an approved value added re-seller and system integrator for the leading VM600 system, Zeefax has gained vast experience in creating systems and managing large amounts of supervisory data; to compliment the systems, Zeefax has created this advanced vibration analysis toolkit which is available to all users of the VM600 systems.
VibraTool™ is a fully integrated and comprehensive utility for creating and managing databases, and for analyzing, viewing and printing plant vibration and supervisory data. This simple to use tool dovetails perfectly into any VM600 system and complements the standard reporting and analysis tools provided with the system.
VibraTool™ includes all the options for creating and managing a new database, and importantly, it has a range of utilities for database record management, including tools for thinning, copying and deleting data from large databases.
.More about VibraTool™ – click here
OPCWhether you are looking for simple off-the-shelf solutions or a complete turnkey installation, the services we provide excel in meeting the specific OPC requirements of our customers.
What is OPC?
OPC is a set of standards that allow data to be shared transparently between various different hardware and software platforms.
The OPC Server, the OPC Client and the OPC driver of PowerPAC™ provided by Zeefax are fully compliant with the original Data Access Specification, but also support all other variant OPC specifications simultaneously.
We provide OPC Server and OPC Client solutions globally to other system integrators, manufacturers, and end-users, and our Power-Packed OPC Solutions™ primarily involve supporting the OPC Data Access Specification in conjunction with data acquisition using our PowerPAC™ data acquisition software product.
Benefits of OPC
A significant benefit of employing OPC Server and OPC Client solutions is that the hundreds or even thousands of temperature, pressures, overall, static and dynamic data measurements can be made and viewed at multiple locations throughout a given site with standard software from many vendors.
Use our Experience
We have decades of experience in data acquisition, vibration monitoring, system design, integration, and deployment in many industries including the utilities and manufacturing.
Providing Power-Packed OPC Solutions™ to end users, 3rd party integrators and manufacturers is our business, and total customer satisfaction with system reliability and rapid cycle time from specification to deployment is our goal.
IMPView®Zeefax has introduced a new software product to accompany the 35954U S-Net-to-USB interface, and have branded it using the established IMPView® name, which was originally owned and used by Solartron, and which is now owned by Zeefax under the technology transfer agreement recently completed between Zeefax and Mobrey.
The new IMPView® for Windows™ is a configuration, test and data transfer tool designed to allow both existing users and those intending to install new Isolated Measurement Pod (IMP) based data acquisition networks, to use IMPs with modern processor technology. It also includes data sharing and translation using industry standard data protocols – including OPC and MODBUS – to external historians and data collectors.
The new IMPView® supports multiple 35954U units into multiple USB ports on a single machine, thereby providing a device for consolidation, manipulation and re-transmission of a combination of acquired data from multiple existing – or new – S-Net networks.
More about IMPView® – click here
VM600 TSI SystemsThe VM600 System from VibroMeter
The VM600 System from the VibroMeter division of Meggitt Sensing Systems inc. (MSSi) is a computerized online Vibration Analysis and Condition Monitoring solution for both critical and non-critical rotating machinery, and is used for early identification of developing machine faults, optimizing performance and improving maintenance planning. It typically forms the field data interface and central processing hub of our fully engineered systems.
This fully integrated total monitoring system offers a powerful combination of dynamic and static measurement capability, designed to meet the requirements (API670) for protection and monitoring of large turbo machinery. It is therefore perfectly suited for use in power generating stations featuring large steam or gas turbine units, and also for protection and analysis of critical plant items in and around petrochemical and process installations. Based on a VME backplane, the system incorporates a range of machinery functions, including full protection and shut-down as well as multichannel condition monitoring and diagnostic capabilities.
It is also worth noting that the VM600 is scalable, and allows simultaneous monitoring of multiple machines within a single system, and therefore it is as much at home for monitoring numerous smaller, perhaps less critical, plant items, in conjunction with or side-by-side with any major plant items.
Key Features
- Modern state of the art online machinery vibration monitoring and analysis solutions.
- Online vibration and trend analysis enables early identification of developing faults.
- Condition based maintenance program reduces unscheduled downtime and improves materials and resource planning.
- Applications include large steam turbines, and associated pumps, compressors and fans.
35954U USB Interface ModuleThe SNet-to-USB interface unit, designated the 35954U, is designed to allow users of modern processor technology, including Laptops fitted with universal interface bus technology, to continue to take full advantage of the robust and well proven IMP/IMC based data acquisition technology.
.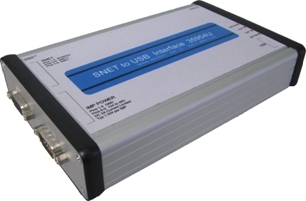
More about the 35954U SNet-to-USB interface – click here
.
35954C PCI Bus Interface CardOriginally design by Solartron Instruments back in the 1980s, Zeefax has recently acquired the IPR for the whole range of IMP products, and now are able to offer new manufactured SNet interface cards for both legacy and new users of the IMP system.
Two interface options are available for use with the SNet system, consisting of the re-engineered 35954C bus adaptor card and the 35954U SNet-to-USB interface.
These two provide a choice for existing IMP system users who wish to upgrade their host computer systems, whilst still retaining the use of an existing SNet installation.
More about the 35954C SNet interface card – click here
SNet CommunicationsThe SNet is a high speed industrial digital communications network, performing three main functions for the IMP network; not only does it provide parameter setting and control, but it handles all data transfer back to the host computer and the single twisted pair network is also used to provide energisation power to all the pods on the network.
A single SNet segment can be up to 1 mile (1.5 km) long and up to 50 IMP/IMCs can be multi-dropped at any location along its length.
The SNet provides excellent noise rejection with transparent error correction, and the cable requires only two conductors, giving ultra-low cost installation and maintenance.
Two SNet interface options are available; the 35954C Interface card and the 35954U interface module; please click the options opposite for more details.
Probe Calibration, Supply & Repair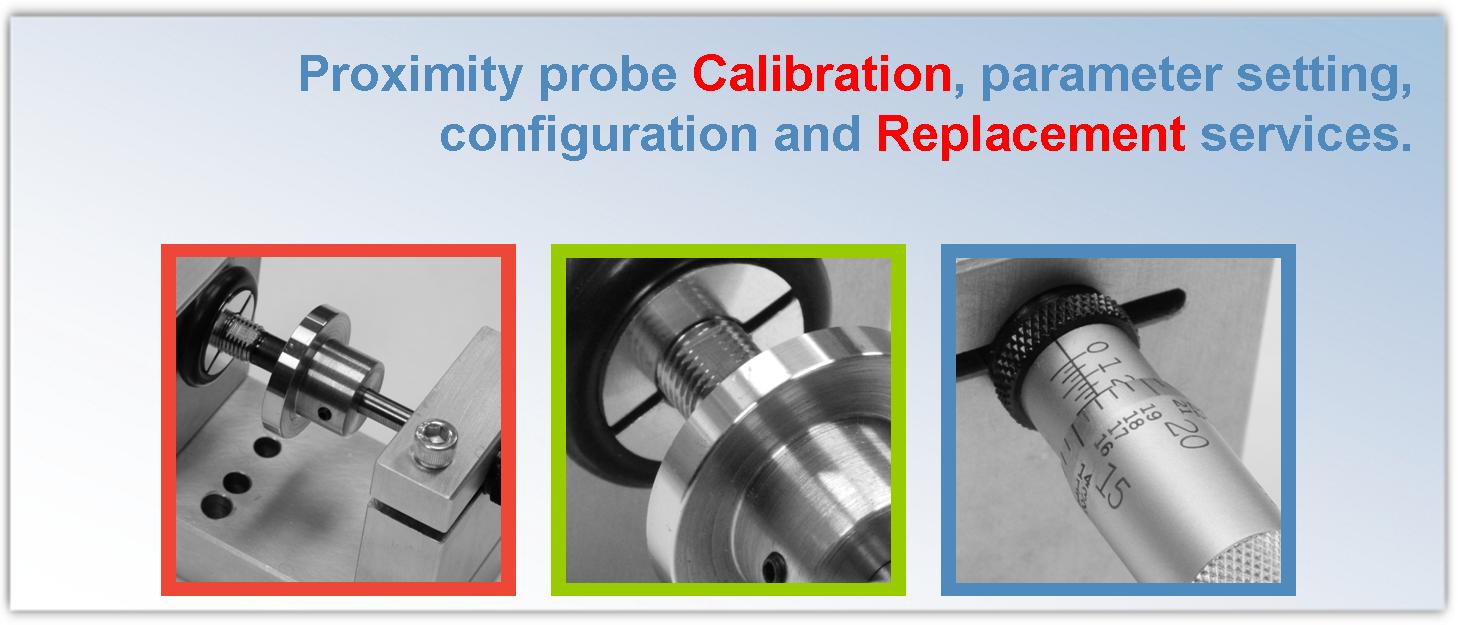
We believe that the sensor or transducer is one of the most important parts of any system, yet sadly, it is often the part which is neglected in the rush to meet outage deadlines and close a unit following overhaul or outage. It is therefore vital that sensors should be carefully maintained and checked periodically to ensure continued good calibration and operation.
To this end, Zeefax provide a periodic re-calibration, repair and replacement service, intended to ensure that the most important part of any system – the probes – remain in good working order.
These services are not only available to existing customers to whom we may have sold complete systems, but also to any instrumentation user who may require support and assistance from time to time with eddy probe and sensor calibration, parameter setting, fault finding and replacement.
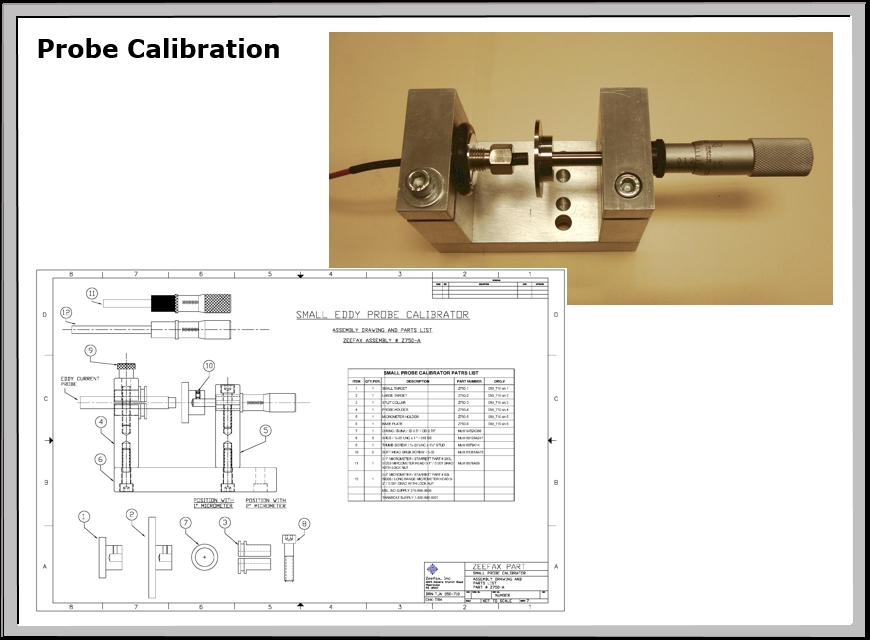
Regular probe calibration, assessment and/or repair will ensure continued fault free operation, not only of the probes themselves, but also of the whole system which they feed.
Bad data in – bad reports out !
Applications and DiagnosticsThe University of Life teaches us that, ironically, the most important things to do are often the hardest things to do – just try asking any politician about this! Similarly, experience in the field of working on turbine supervisory instrumentation projects, shows that it is sometimes the most important parameters to be measured which are the hardest to get right. Paradoxically, it also seems that these parameters are at best, given scant consideration, and at worst, they are overlooked altogether until the last moment, just before the turbine is being closed up, or just as it is about to be run, when it is often then too late.
The key turbine parameters of Thrust, Differential Expansion and Case Expansion can have such an impact on the efficient operation and on the general health of the machinery being monitored that it is clearly an anomaly that these parameters are probably the least understood of the TSI parameters. The reasons for this are probably many, not least that the other main parameters of Vibration, Temperature and Valve Position are easier to set up, and are well established and documented. Other historical and anecdotal evidence points to a general scarcity of knowledge and understanding as to the benefits and pitfalls associated with measuring these parameters.
Lack of ownership of the supervisory system is often cited as the reason for this, with no clear responsibility being taken either for the collation of relevant information or for making appropriate allowance in the outage schedule. This is particularly the case for the differential expansion, the setting and checking of which is necessarily time consuming and often requires mechanical and electrical support from outage engineers.
These articles are intended to provide some insight and to clarify the requirements and to highlight the pitfalls associated with measuring Thrust, Differential Expansion and Case Expansion, which will, it is hoped, lead to a more proactive approach towards them, thereby ensuring that they are adequately provided for in any project schedule.
This list of available articles is not exhaustive and will be subject to revisions and additions from time to time as and when they become available, so please visit this page again regularly.
We produce new articles based on customer feedback and in response to specific requests for assistance. Therefore, if you would like any specific help on any topic either listed here or not listed here, please contact us via our contact page and we will try to help.
Articles and DocumentsTurbine Supervisory SystemsMachinery is under stress
In modern power plants, units are often cycled much more frequently than originally designed for; this may be to conserve fuel or to meet load scheduling or environmental requirements, but as a result, rotating machinery is typically under higher levels of mechanical stress than in previous times, and much more detailed machinery condition and performance information is required in order to operate safely and efficiently.
On most rotating equipment, shaft vibration and position information – such as Rotor Expansion, Casing Expansion and Differential Expansion – provides a good indication of a machine’s normal operating fingerprint or signature, which is required in order to recognize any changes which might occur with time. Early recognition and analysis of changes is vital and allows for well informed decisions to be made, for example, whether to shut down immediately or to wait until the next scheduled outage. However, modern instruments can provide a great deal more information relating to the condition of the machine components, including detecting broken or cracked shafts, seal rubs, looseness or misalignment. These conditions can be detected and monitored as they develop, leading to informed operational and maintenance decisions.
Costs and Benefits
The benefits of a structured Condition Monitoring program supported by well financed and carefully designed TSI systems – including sensors, signal conditioning, data acquisition and analysis software and tools – are well established and documented.
In a detailed study on three identical plants back in the 1970’s, the costs of the three main types of maintenance program indicated that a ‘Run-to-failure’ maintenance program might cost $12-$15 per hp per year and a ‘Preventive’ or ‘Scheduled’ maintenance program might be $8 – $10 per hp per year. But a ‘Predictive’ maintenance program might be in the region of $6 – $8 per hp per year, representing significant cost savings when one considers the large horse-power installed on many sites.
These figures have recently been updated by EPRi, and indicate that for every dollar spent on ‘On Condition’ based maintenance, $1.47 would have been spent on ‘Planned’ or ‘Scheduled’ maintenance and $1.89 would have been spent on a ‘Run-to-failure’ or ‘Breakdown’ maintenance program.
These numbers speak loudly for themselves!
What is TSI ?
Turbine Supervisory Instrumentation (TSI) typically provides plant owners, operators and maintenance groups with the data required for conducting Condition Monitoring studies and structured Predictive Maintenance programs on steam turbine machinery as would usually be found in large power generating plants.
Increased use of TSI and the related availability of detailed knowledge as to the condition of the machinery, typically reduces operating costs by:
- Reducing the time required to start a turbine
- Extending the time intervals between scheduled outages
- Reducing the time taken for repairs by enabling improved parts
- Provisioning and manpower planning
- Providing increased diagnostics and fault finding capabilities
- Giving early warning of developing problems
- Providing automatic shutdown of the units
- Preventing minor problems from becoming catastrophic failures
- Preventing collateral damage as a result of such a failure
- These benefits translate into hard cash when one considers the size of these generating sets and the associated cost of lost production due to unexpected shutdowns, which often dwarfs the other costs of any mechanical repair.
But technical product developments, economic necessities and environmental constraints have meant that the operational and financial benefits of conducting a structured Condition Monitoring and Predictive Maintenance programs are no longer the sole domain of large Power or Process plants.
Condition Monitoring is increasingly successfully adopted in other industries and locations, including Paper Mills, Metal Processing Plants, Hydro Power Plants and for the new generations of Wind Turbines. This is of course particularly relevant if and when the monitored machine is vital or critical to the financial and operational success of the plant or organization.
TSI equipment is available in all flavors, colors and capabilities, since in this business, one size definitely does not fit all.
Therefore, careful selection of products and design of the overall system is vital to the success of the scheme. Indeed, many schemes fail due to incorrect product selection, inadequate design, weak integration and lack of testing, all of which sounds easy on paper, but in reality, it can be a complex process requiring time and expertise resources which many companies and organizations simply do not possess.
PowerPAC™PowerPAC™ is an advanced Data Acquisition and Display software product, designed to meet the rigorous requirements expected from modern Data Acquisition systems. The many configurable features and comprehensive on-line analysis capabilities – including turbine performance, balance-of-plant and emissions indexes – make it ideal for use in process, power and petrochemical plants, but it is equally at home in the laboratory or for specialist research applications.
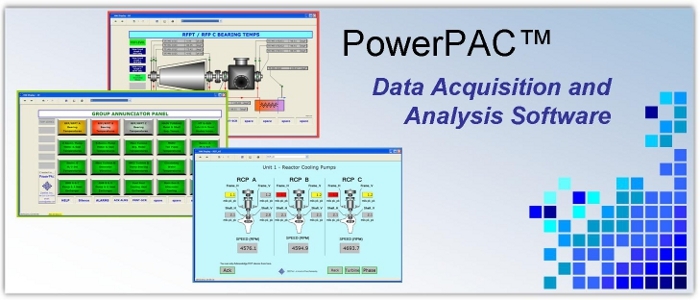
PowerPAC™ is designed for use on PC-based systems running Windows™, and is highly optimized for use within industrial settings. The fully integrated package provides highly versatile and capable data acquisition, for both stand alone applications or when forming part of a larger Turbine Supervisory or general plant monitoring scheme.
Isolated Measurement Pods (IMPs)The Isolated Measurement Pod family (originally designed and manufactured by Solartron Instruments) is the complete solution for distributed measurement challenges.
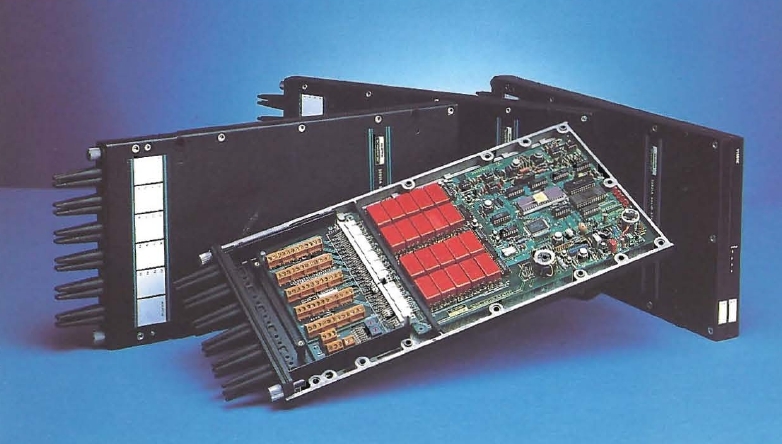
The simple concept means that plant parameters – such as temperature, pressure, position etc. are measured directly at source by intelligent Data Acquisition modules called the Isolated Measurement Pod (IMP). These pods are fully ruggedized for installation directly on plant, and all power and communication is supplied via the single twisted pair network cable.
More about Isolated Measurement Pods – Click here
IMP Features SummaryPrecise….
IMP/IMCs offer accurate, high precision (16-bit) measurements with excellent noise immunity and common mode isolation, even in areas of high electrical interference and vibration. Built-in facilities enhance measurements on thermocouples, PRTs and strain gauges.
Reliable…
With an operating temperature range of -20°C to+70°C (-4°F to +158°F) even at 95% humidity, and a rugged housing meeting IP55 / NEMA 4standards, IMPs are built to work under harsh conditions – whether your plant is hot, dirty, cold or wet – or all four!
Flexible…
Installing the 2-wire multidrop communications network called the S-Net, couldn’t be simpler, and modifications can be made in minutes. IMP/IMCs can be rapidly added or removed when required, without the need for extensive rewiring, and systems can range from just a single IMP/IMC on a single S-Net network up to multiple networks with many thousands of channels.
Cost effective…
IMP/IMCs contain everything you require for precise, reliable data acquisition. What you get is all you need – there’s no necessity for expensive signal conditioning, filters, amplifiers, transducer wiring, vibration mounts, environmental packaging, special power supplies or expensive network hardware.
There are no hidden costs with IMPs!
.
Integral Signal Conditioning
16 bit ADC
S-Net communications and power to host
Built-in sensor energization
Detachable connector block
NEMA 4 / IP55 case (IMP only)
dc voltage, current, temperature
Direct connection to thermocouples or PRTs